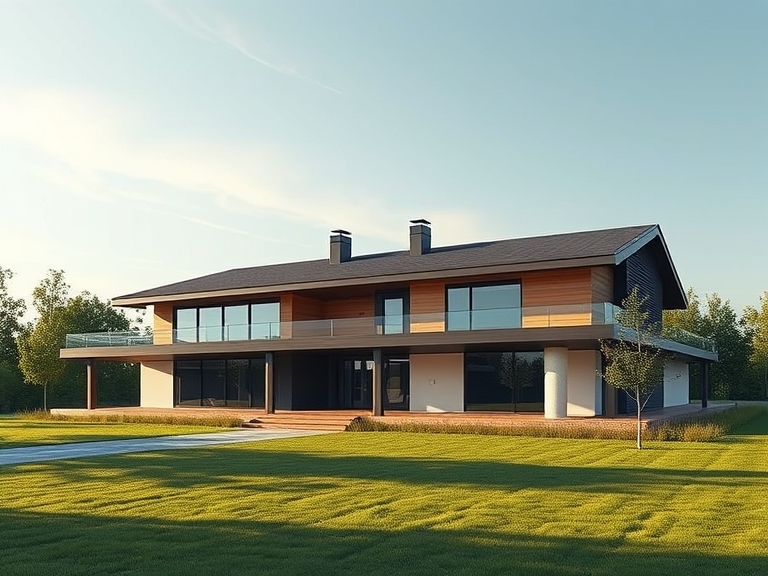
Low slope roofing is a term used to describe roofing systems characterized by a pitch of 3:12 or less, meaning that for every 12 horizontal units, the roof rises no more than 3 vertical units. This configuration distinguishes low slope roofs from steep slope roofs, which possess a pitch greater than 3:12. Understanding low slope roofing is essential for homeowners and builders alike, as it has unique functional attributes and maintenance requirements.
Technical specifications that define low slope roofs include their minimal pitch and the resultant drainage implications. Proper drainage is crucial, as water can accumulate on flat surfaces, leading to potential leaks and structural damage. Low slope roofing systems often include built-in drainage features to facilitate the efficient removal of water. This design minimizes the risk of standing water, which is particularly critical in regions subject to heavy rainfall or snow.
Common materials utilized for low slope roofing encompass a range of options, including single-ply membranes such as TPO (thermoplastic polyolefin) and EPDM (ethylene propylene diene monomer), as well as modified bitumen and built-up roofing systems. Each of these materials offers distinct benefits, such as flexibility, durability, and cost-effectiveness, making them appealing choices for various construction projects.
Additionally, low slope roofing provides numerous advantages compared to traditional steep slope methods. These roofs generally require less material and labor for installation, leading to cost savings. Low slope roofing also allows for expansive rooftop spaces that can be utilized for various purposes, including green roofs, solar panel installations, or recreational areas. This innovative roofing solution combines functionality with aesthetic appeal, ensuring a comprehensive understanding of low slope roofing can inform effective decision-making for construction and renovation projects alike.
Types of Low Slope Roofing Materials
When considering low slope roofing, various materials come into play, each with distinct characteristics that cater to specific needs. One of the most traditional options is Built-Up Roofing (BUR). This system consists of multiple layers of bitumen and reinforcing fabrics, providing robust waterproofing. Its advantages include durability and low maintenance requirements, although BUR can be heavy and labor-intensive to install.
Modified Bitumen is another popular choice for low slope roofing. This material builds upon the concept of BUR but incorporates polymers to enhance flexibility and performance. It typically comes in rolls and is applied using heat or cold adhesive methods. Modified Bitumen is known for its adaptability to temperature fluctuations, although its initial installation costs can be higher than some alternatives.
EPDM (Ethylene Propylene Diene Monomer) is a widely utilized single-ply roofing option known for its excellent weather resistance and ease of installation. Its black or white membrane options provide effective UV protection, contributing to energy savings. Despite its popularity, EPDM may require periodic maintenance to prevent seam separation and ensure longevity.
Another single-ply option is TPO (Thermoplastic Olefin), recognized for its energy efficiency and cost-effectiveness. TPO roofs are typically reflective, reducing cooling costs in warm climates. However, their long-term performance can vary based on the quality of the material used, necessitating thorough supplier research.
PVC (Polyvinyl Chloride) roofing is similar to TPO but offers superior durability and chemical resistance, making it ideal for commercial applications. While its lifespan can exceed that of other materials, the cost might deter some property owners. Each of these materials presents unique advantages and disadvantages, making it crucial to assess specific project needs when understanding low slope roofing options.
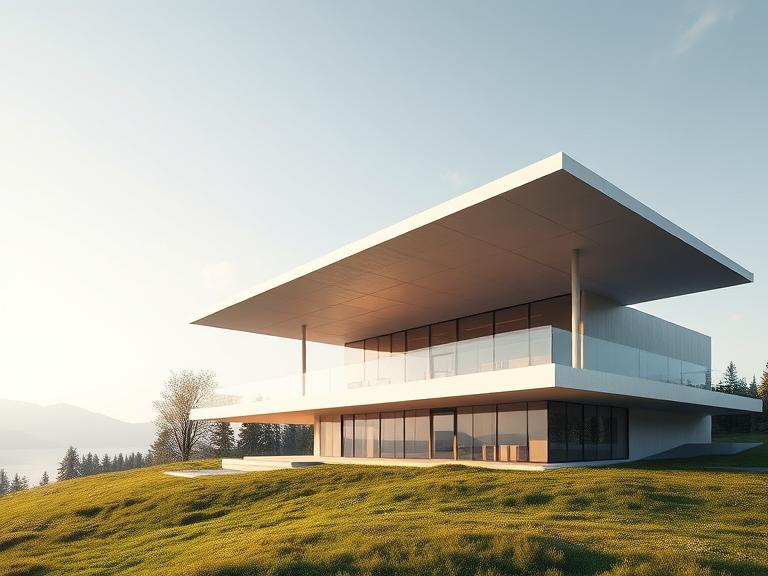
Installation Techniques for Low Slope Roofing
Low slope roofing systems present unique challenges and opportunities in installation, necessitating a precise approach to ensure longevity and optimal performance. Selecting the appropriate installation technique is critical, as improper methods can lead to significant issues, including leaks and structural damage. There are several prevalent materials used in low slope roofing, including built-up roofing (BUR), modified bitumen, and single-ply membranes such as TPO and EPDM. Each of these materials requires specific installation steps and techniques.
For built-up roofing, the installation typically involves layering alternating layers of bitumen and felts. It is essential to ensure that each layer is adequately adhered and sealed to prevent moisture ingress, which could compromise the roof’s integrity. This method results in a durable, multi-layered roofing system; however, it demands precise handling of hot materials and adherence to safety protocols during application.
Modified bitumen roofing, often installed using either the torch-applied method or cold adhesive, is another common choice for low slope roofs. This roofing material requires careful application to ensure that seams are properly sealed, as the integrity of these seams significantly affects the roofing system’s performance. Employing the torch-applied method requires skilled labor to prevent fire hazards and achieve optimal bonding.
Single-ply membranes are growing in popularity due to their ease of installation and lightweight properties. They are often mechanically attached, adhered, or ballasted, depending on the specific product chosen. Understanding low slope roofing requires knowledge of these installation methods to achieve an effective roof. Regardless of the chosen method, it is crucial to avoid common mistakes such as inadequate drainage planning or neglecting proper seam sealing, which can lead to future complications.
Ultimately, hiring skilled professionals with expertise in low slope roofing installation is paramount. Proper training and experience significantly enhance the quality of the installation and ensure that the roofing system functions effectively over its lifespan.
Maintenance and Repair of Low Slope Roofs
Maintaining low slope roofing systems requires a proactive approach to ensure their longevity and functionality. Regular inspections are essential, ideally performed at least twice a year, as well as after significant weather events. These inspections should focus on key areas such as seams, flashing, and drainage systems. Identifying potential issues early on can help property owners address concerns before they escalate into major problems.
Common issues with low slope roofs include ponding water, membrane damage, and debris accumulation. Ponding water, which occurs when water collects on the roof instead of draining properly, can lead to structural integrity issues and should be addressed promptly. Regularly clearing debris, such as leaves and twigs, from drainage areas will facilitate proper water flow and help prevent ponding. Additionally, checking the roof membrane for cracks or blisters can thwart leaks before they become a significant concern.
When dealing with leaks or damage, it is crucial to act swiftly. Small leaks can often be repaired by applying liquid roofing or patching materials, while more extensive damage may require more significant interventions. In cases where specialized repairs are needed or if the damage is beyond the homeowner’s capability, seeking professional assistance is advisable. A qualified roofing contractor with experience in low slope roofing can accurately diagnose problems and recommend the best course of action.
Overall, the maintenance and repair of low slope roofs should be treated as a preventative measure rather than a reaction to potential issues. By adhering to a regular maintenance schedule, addressing common roofing problems proactively, and knowing when to request professional help, property owners can significantly extend the lifespan of their roofing systems. Understanding low slope roofing maintenance not only safeguards the structure of the building but also prevents costly repairs in the future.